Space Park Leicester
Client: University of Leicester
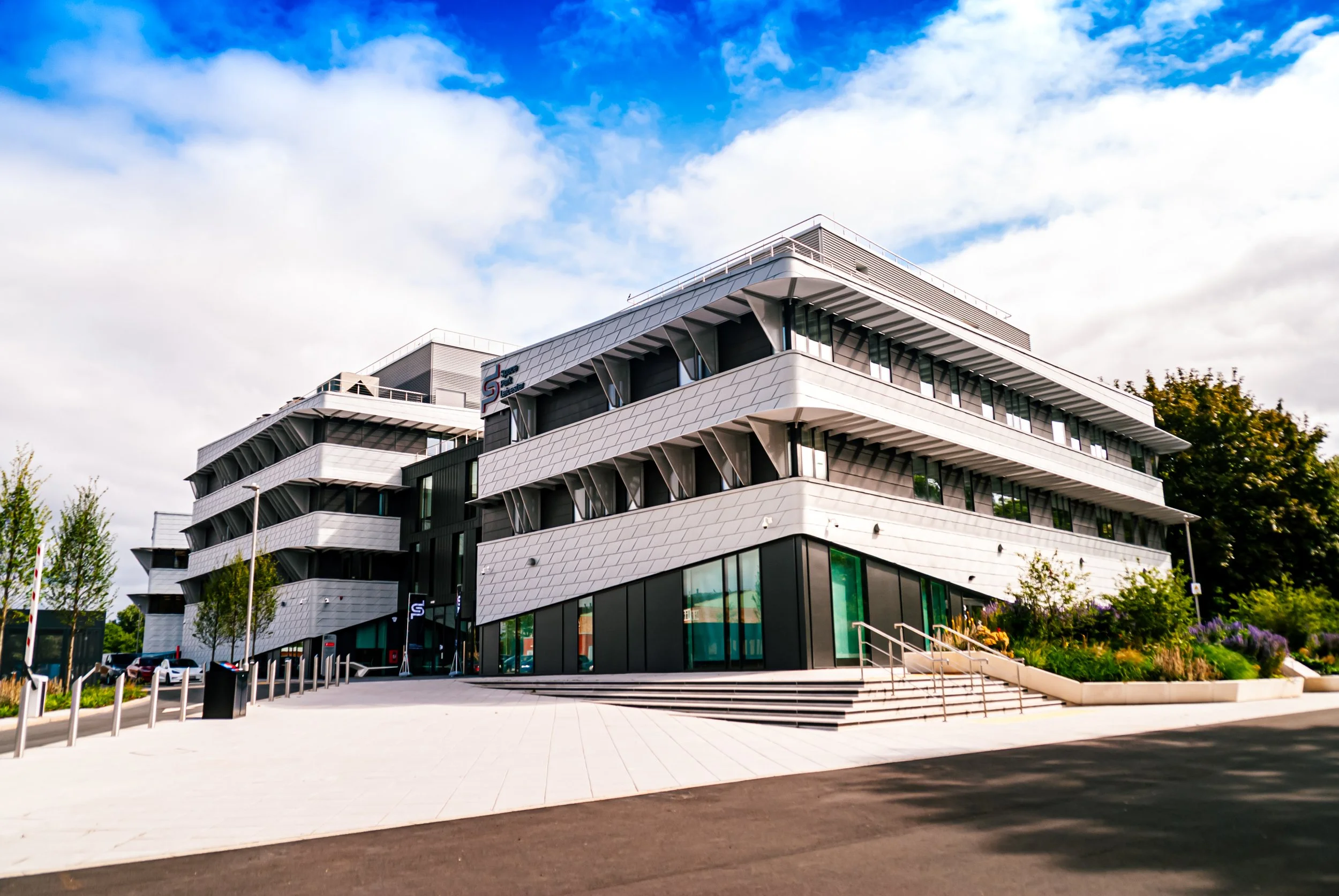
Our Approach
The brief
Space Park Leicester is a state-of-the-art research, development, and manufacturing facility, with offices, laboratories, teaching facilities and co-working spaces all focusing on driving growth in the space sector.
Delivered for the University of Leicester, CPW joined the £46.4 million project in 2019 to deliver the mechanical and electrical engineering consultancy services, as well as undertake a site monitoring role.
The 10,700 m² facility transformed a long disused and contaminated brownfield site, formerly used for landfill, into a major generator of social, economic, and environmental improvement.
The project is set to contribute £750 million a year to the UK space sector, including more than 2,500 direct and indirect jobs across the East Midlands.
Complex considerations
The scheme was delivered within budget and on time, despite the challenges of the Covid-19 pandemic and the complexities of the project.
The development included a number of highly technical spaces with specific and challenging requirements. This included the Satellite Engineering and Test Laboratory (an ISO 6 clean room with ISO 8 robing room), four double height flexible engineering laboratories linked by overhead crane which can be combined or used separately, dark laboratory and virtual reality cave, Wolfson laboratory, model workshop, metrology laboratory, and mechanical and electronics workshops. Effective stakeholder engagement, with the academic and estates teams within the University and with external partners, was essential to agreeing the configuration of these spaces.
The mechanical team was heavily involved throughout phase two design and construction. Holding weekly client meetings, CPW ascertained the requirements of the various spaces within the facility as the specialist areas were incredibly complex.
A forward-thinking strategy was implemented, using air source heat pumps (ASHP) for most of the heating season, supplemented by gas boilers that only operate during the depths of winter (when ASHP would be inefficient) or when is a problem with the heat pumps.
The project also included dedicated ventilation plant for the ISO classification 6 standard clean room and oxygen depletion systems, as well as gas systems, compressed air systems, and close controlled air systems for the labs.
From an electrical point of view, given the number of high-tech spaces in this large building, the team had to design infrastructure that was able to cope with the amount of power required. As a result, £2 million worth of electrical infrastructure was installed and supplementary energy sources such as solar PV were installed on the roof.
Challenges
Close contact with the estates team and was essential to keep the project on track and clearly define the end users of each space. This is a common challenge with large buildings where requirements may not be set from the outset of the project, but the team ensured the optimal environment was created to meet the requirements of each space and engaged with a large number of stakeholders thanks to wide ranging interest in the project.
Disruption from the Covid-19 pandemic created uncertainty with lead times and project continuation – calling for increased adaptability. Despite this, there was no significant delay to the project, even with new build aspects, such as the ISO 6 clean room, introduced late on in the scheme.
Energy performance certificate: A
ProCon Leicestershire Awards 2022: Large Non-Residential Scheme of the Year Award
ProCon Leicestershire Awards 2022: Regeneration Project of the Year
East Midlands Property Awards 2022: Sustainable Projects of the Year
Want to find out how we could support your project? Visit our services page.